Take it from one now immersed in manufacturing – making things is an epic process of production, delays, shipping, customs… 3D printing is the latest DIY technology to promise to get around that, armed by the seemingly-magical translation of digital files into objects in a way other machines cannot. We’ll be looking in depth at what 3D printing can mean for music starting next week, as interest in this technology reaches fever pitch, but here are a couple of revealing case studies.
For Teenage Engineering, makers of the OP-1 synthesizer, 3D printing seems to be a real breakthrough. Their line of accessories was a clever line of mechanical cranks and LEGO Mindstorms attachments, ingenious applications of little pieces of plastic. There was just one problem: shipping costs made these accessories too expensive, and customers complained. TE responded by posting CAD files. Head to Shapeways, and you can print these parts on a 3D printer for a small price. TE has gotten plenty of attention from the media as perhaps the first to go this route. [See Wired] (I suspect replacement parts are not something new – but going the 3D printing route perhaps is, a sign of just how new this medium is as far as mainstream adoption.)
In fact, the results are so clever, I can imagine small manufacturers now looking for ways of replicating the success – considering designs they might not have otherwise.
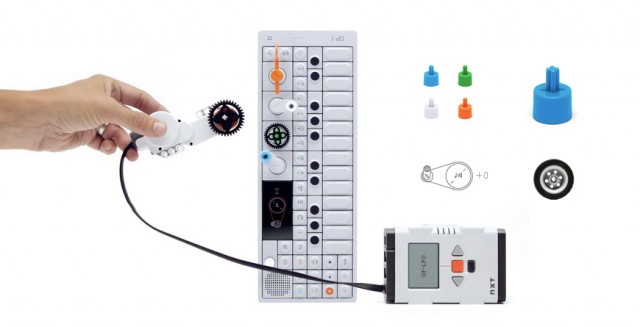
Clever, small accessories proved to be too small – racking up shipping costs – until TE experimented with letting users 3D-print their own accessories and replacement parts.
3D printing isn’t always a panacea, however: it could be both exciting and maddening at once.
Teague Labs suggests a far more ambitious project: printable headphones.
After all, headphones are largely about the physical construction; the actual sound-producing transducer element is reasonably simple. The Teague headphones are special on a number of levels. They are a complete pair of headphones with a nice-looking design, a complete product that needs only a small amount of electronics and prints the rest on a 3D printer. But even more compelling is the breakthrough application of a pro design to a hobbyist printer. Teague began with a professional ABS FDM machine, but adapted the same design to the far more-accessible Makerbot Replicator.
Prototype as Product: 13:30 Printable Headphones [Teague Labs]
13:30 Headphones at Thingiverse
via PSFK
Just don’t get too excited, too fast. Traditional materials still offer potential that the actual substance of a 3D printer can’t match. Hobbyist printers pose their own challenges: I spoke to a 3D printing marketplace rep this week who explained to me that the fact that 3D printers aren’t running all the time in hobbyist environments causes clogs and breakdowns to become far more frequent, something you probably don’t think about. (Turns out, your inkjet printer suffers from the same problem; it’s just that ink is an easier problem to fix.)
And be prepared to wait – not only for the advancement of 3D printing, but for the model itself. These headphones take over 13 hours. That means 13 hours of printing time. Again, you see the advantage of injection molding: prepare the mold once, and then reproducing the item is fast and cost-effective, meaning that 3D printing will largely be advantageous for something that needs to be customized (and thus not replicated en masse in quantity), or something that’s easier to print on-site than ship. Correction: Apparently breathing some sort of plastic fumes, I incorrectly suggested some substantial cost. Rather than get that wrong, we’ll go into the cost issue soon as we look at one venue – Berlin’s Betahaus – that’s setting up a “fab cafe” that makes 3d printing as easy as buying an espresso. (In fact, they have espresso, too.)

Now, you can become your own headphones maker – and 3D print complex forms, easily. Just be prepared to wait about half a day on the printer.
At the same time, I love the way Teague articulates the underlying idea here:
With 3D printers becoming more accessible we decided to have a think around the concept “life in beta” as a future scenario. What if printed prototypes could become actual products? Meaning, once off the print bed an object could be assembled without any tools and be made functional by readily attainable components. I decided to stress test the premise with the challenge of making electronically simple yet functionally complex headphones.
There’s plenty to explore here, even without waiting for costs to come down and printers to get better and more affordable. (Oh, yeah, and – those things don’t just happen magically. They represent an engineering challenge a lot of people are tackling. So it’s best, I think, to look at what’s possible right now. And that turns out to be a lot.)
After all, the fact that Teenage Engineering made some clever accessories more affordable demonstrates that this doesn’t have to be a dream, after all.
Join us next week and in the near future as we look more at 3D printing advances with our summer industrial design intern and other experts in the field. Have a good weekend, and see you Monday.